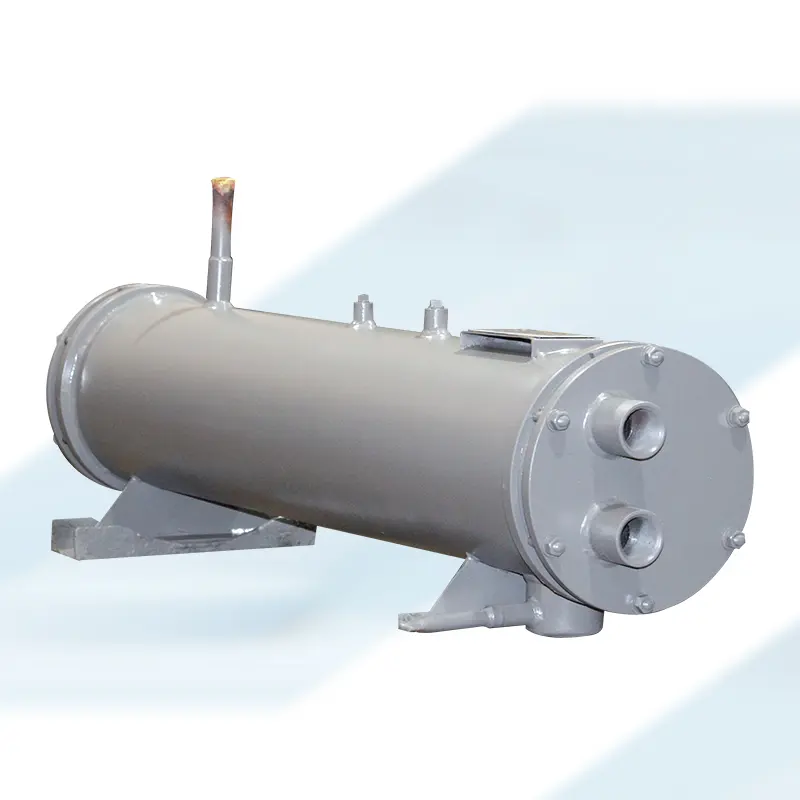
Elevate Your Cooling Processes With Our Copper Tube Condenser
Copper tube condenser marked a significant leap forward in the realm of heat exchange technology. Its inception revolutionized various industries, particularly in air conditioning and refrigeration systems. The copper tube condenser stands as a cornerstone in modern HVAC systems, embodying a harmonious blend of efficiency, durability, and practicality.
At Abe & Hex India Private Limited, we take pride in being the leading manufacturers and suppliers of top-tier Copper Tube Condensers in India. Our unwavering commitment to excellence has earned us the trust and appreciation of countless customers.
As leading Copper Tube Condenser Manufacturers in India, we use only the finest raw materials, meticulously sourced from trusted vendors in the market. We use copper as the primary material to build these tube condensers due to its high thermal conductivity for heat transfer.
PRODUCTS GALLERY


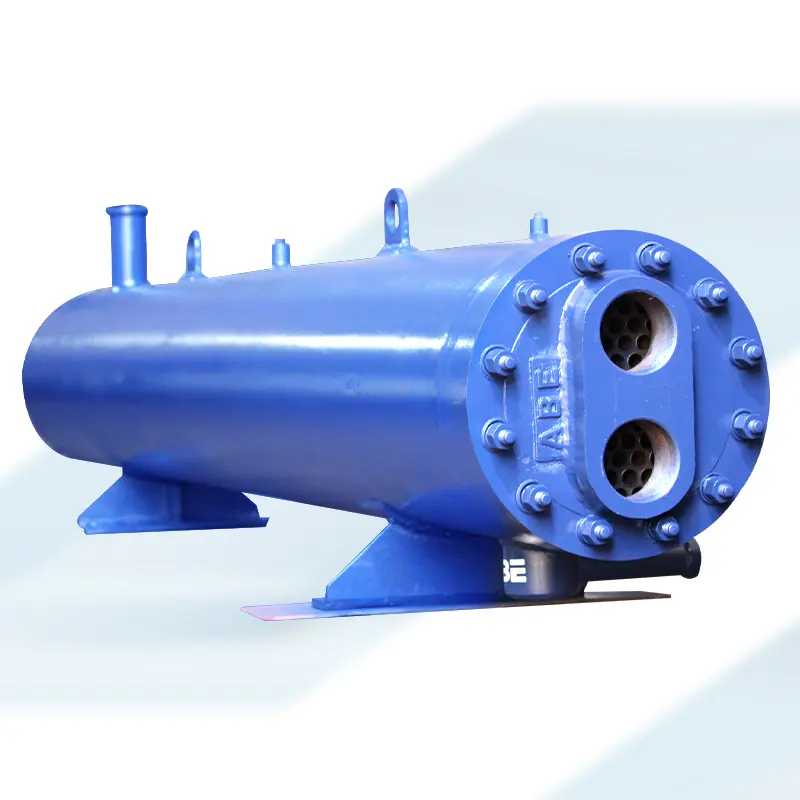
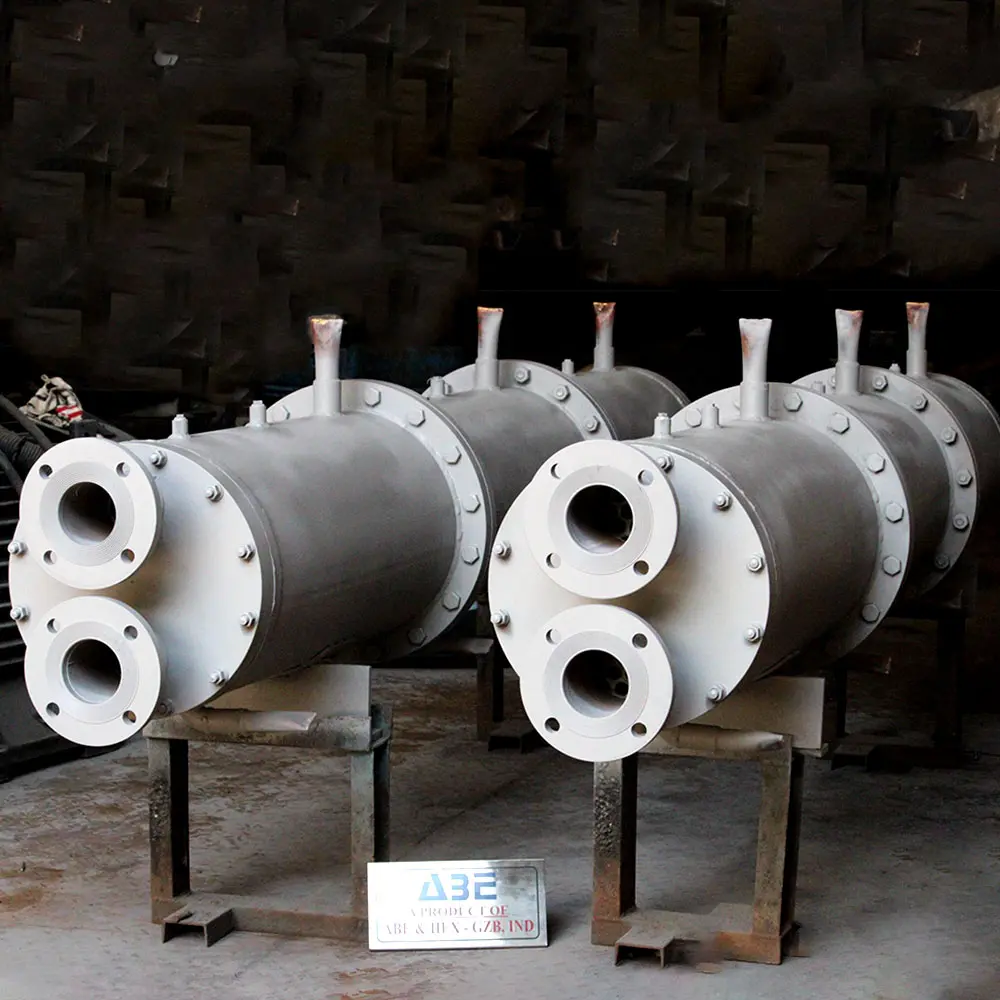
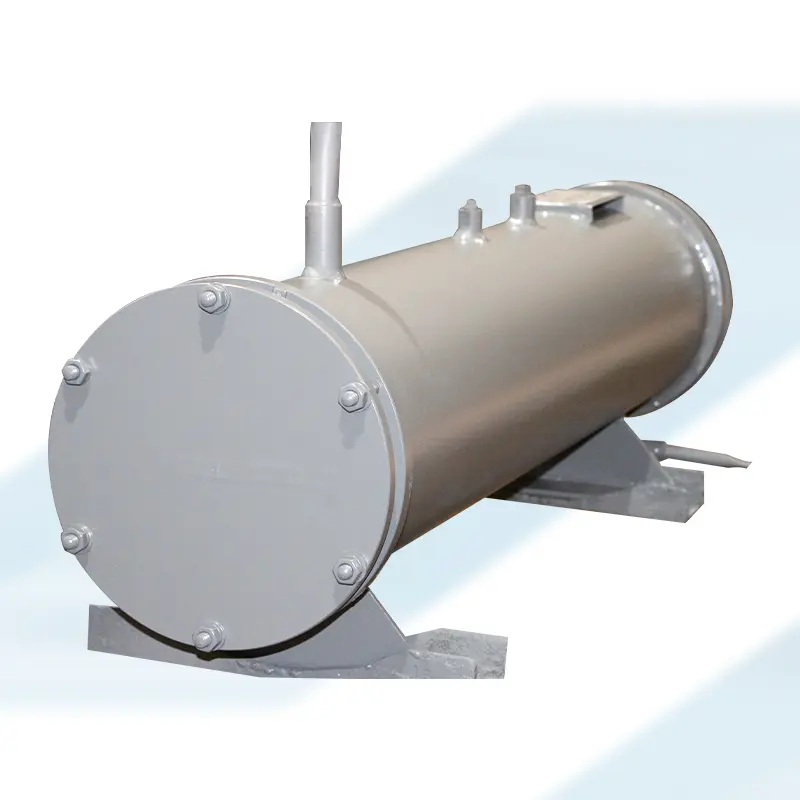
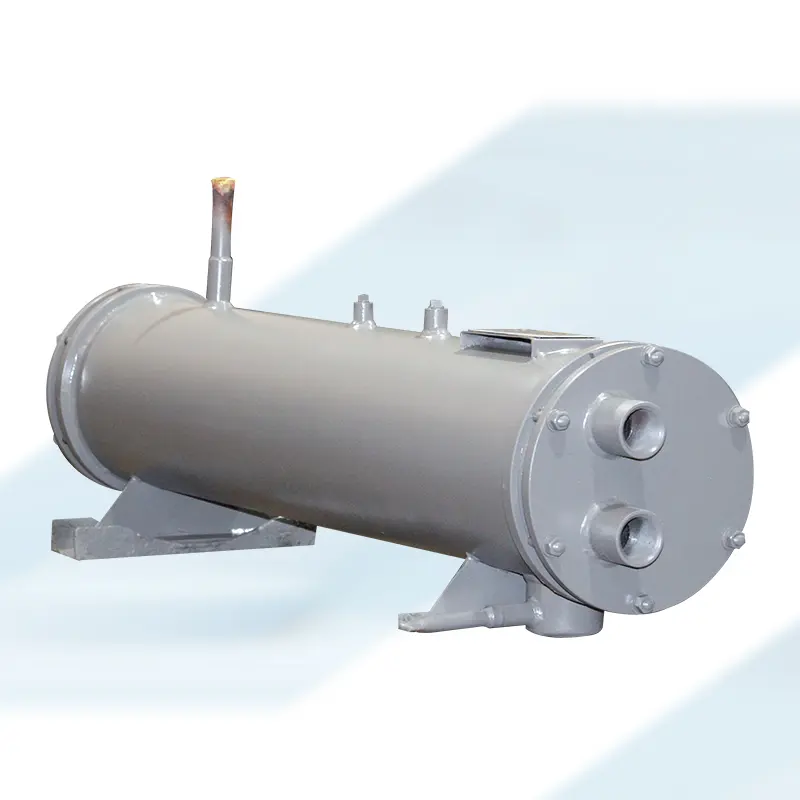
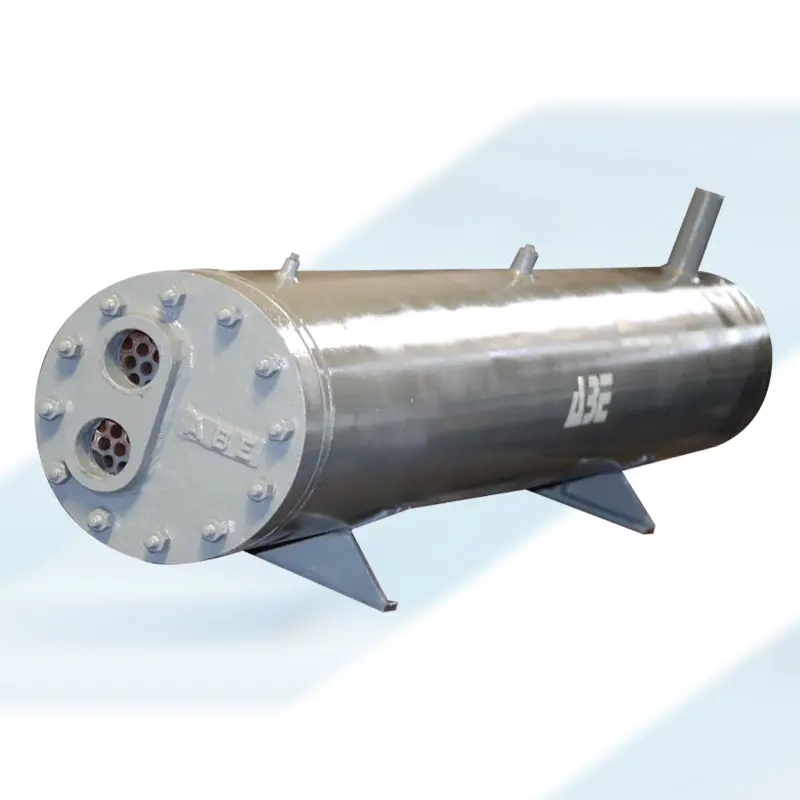
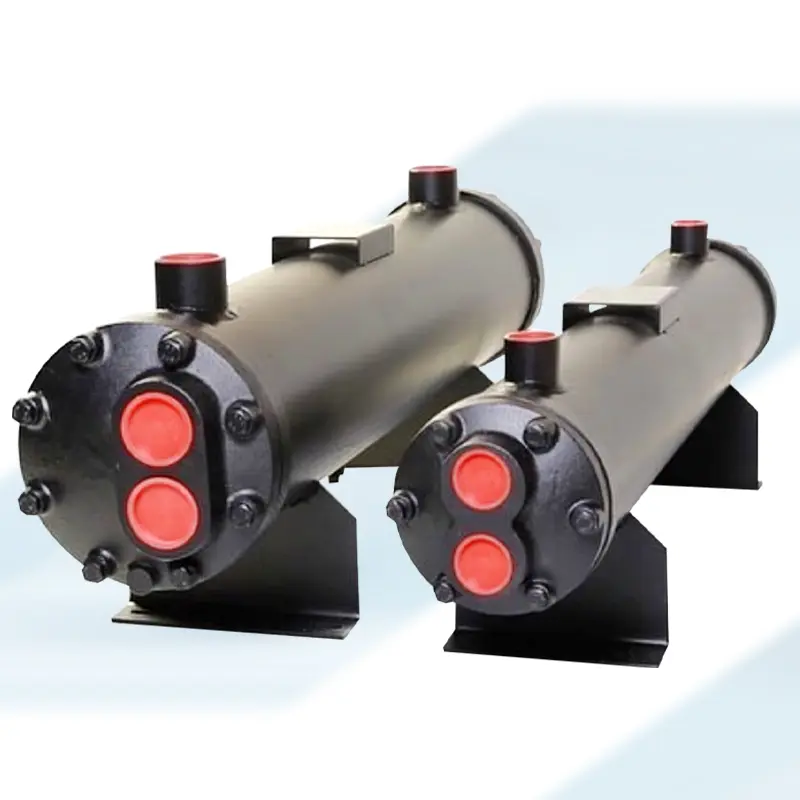
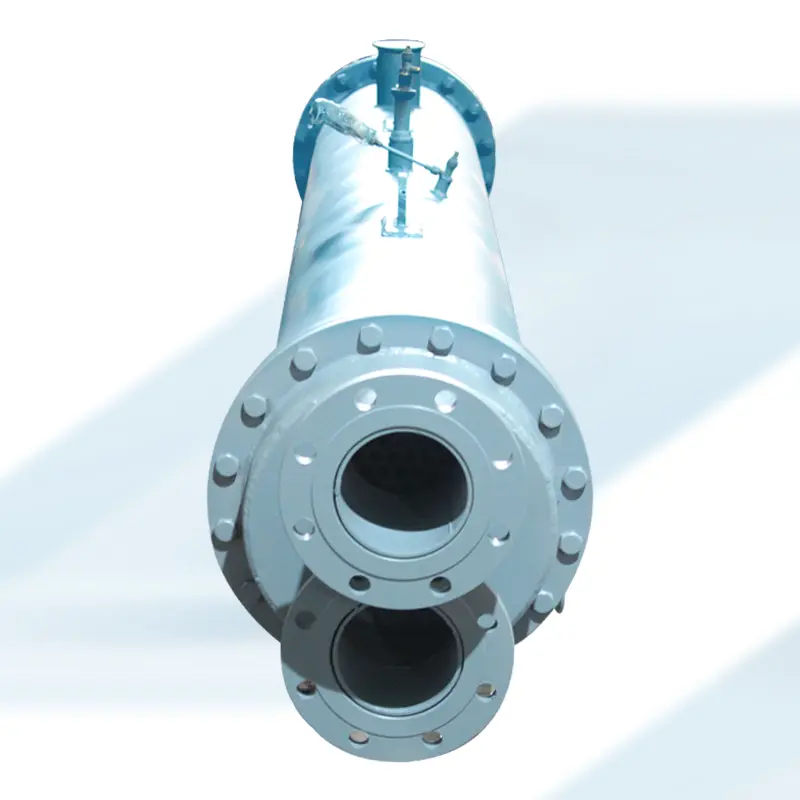
Choose From the Top Brands of Copper Tube Condenser!
With our state-of-the-art technology and skilled craftsmanship, we deliver condensers that excel in efficiency and reliability. Compliance with stringent industrial standards is a cornerstone of our manufacturing process. If you need high-quality tube condensers for your unique requirements, we have got you covered.
We are one of the top Copper Tube Condenser Suppliers in India, offering tailored solutions to meet your exact specifications. Elevate your cooling systems with our unparalleled Copper Tube Condensers – where quality meets innovation. Contact us today to learn more about our range of copper tube condensers.
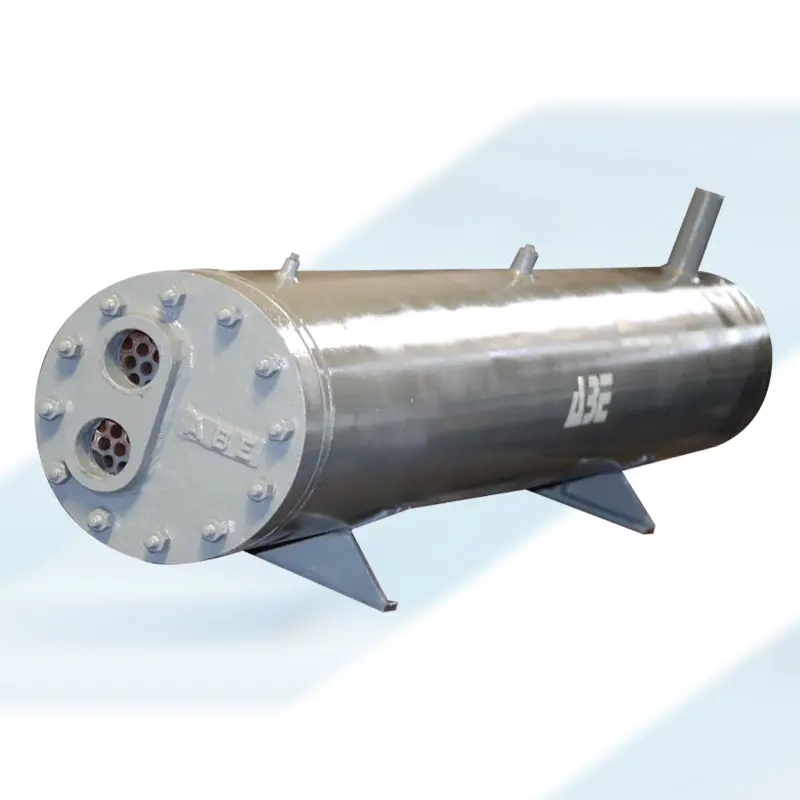
Key Features
- Robust construction
- Unmatched durability
- Double tube configuration
- Resistance against corrosion
- Compact and low-maintenance
- Maximized surface area contact
- Unparalleled heat transfer capabilities
- Crafted from premium-grade stainless steel
- Tube-in-tube design for optimized heat exchange
Applications
- Power Plants
- HVAC Systems
- Petrochemical Industry
- Chemical Processing Plants
- The food and Beverage Industry
- Brewing and Distilling Applications
- Food Processing and Preservation
- Pharmaceutical Manufacturing Sector
- Refrigeration and Air Conditioning Systems
SPECIFICATIONS
Ensure the condenser’s capacity is in harmony with the chiller system’s cooling load, typically gauged in tons or kilowatts.
When it comes to shell and tube condensers, the tube layout is subject to change, be it finned or smooth tubes, based on the efficiency and heat transfer specifications.
The efficiency of water-cooled condensers hinges on water quality. It’s imperative to vigilantly oversee and uphold the excellence of the cooling water to steer clear of problems such as scaling or corrosion.
- Shell and Tube Condenser: Within this conventional condenser, the refrigerant moves through the tubes, while water travels across them in a shell.
- Plate Heat Exchanger: In specific chiller setups, condensing duties are performed by plate heat exchangers, known for their efficiency and space-saving design.
Explore energy-conscious designs and functionalities to lower operational expenditures.
The condenser should be appropriately sized and its physical dimensions should be well-suited to the space provided in the chiller plant.
Design the water-cooled condenser to handle a particular flow rate of cooling water, determined by the chiller’s capacity and the desired temperature difference.
Examine if the condenser includes built-in controls and monitoring systems to enhance operational efficiency and facilitate swift fault detection.
Fans or pumps may be essential in certain condenser designs to aid in heat exchange or regulate water flow effectively.
Materials like copper, aluminum, or stainless steel, which are resistant to corrosion, are typically used in the construction of the condenser.
Make sure to consistently abide by the manufacturer’s recommendations for installation, operation, and upkeep.
Designed with precision, the condenser’s heat transfer surface area optimizes the process of transferring heat from the refrigerant to the cooling water.
Facilitating effortless entry to the condenser for maintenance and cleaning is vital in maintaining its performance and extending its lifespan.
Confirm that the condenser aligns with the specific refrigerant utilized in the chiller system.
Make certain the condenser meets all environmental regulations and safety protocols.
Designed with specific connections for refrigerant flow, this condenser guarantees a smooth and controlled movement of refrigerant through the system.
This condenser is furnished with access points for both the supply and return of cooling water.