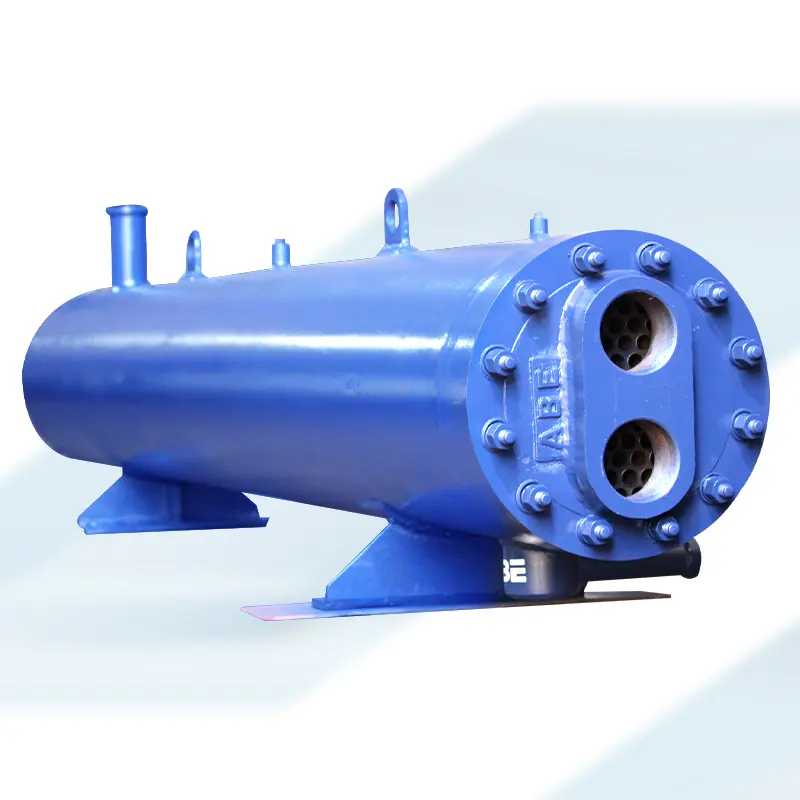
Horizontal Shell and Tube Condenser: Made With Robust & Durable Metals
When it comes to industrial processes that involve the transfer of heat, having a reliable and efficient condenser is crucial. One popular choice for this purpose is the Horizontal Shell and Tube Condenser. This ingeniously designed heat exchange system plays a pivotal role in various applications, ensuring optimal cooling performance.
A Horizontal Shell and Tube Condenser is a specialized heat exchanger that facilitates the efficient transfer of heat from a hot fluid to a cooler fluid. It’s designed to efficiently convert high-temperature vapor into a condensed liquid form.
If you are searching for high-quality horizontal tube condensers, your search ends here. We are one of the top Horizontal Shell and Tube Condenser Manufacturers in India, offering these products in various specifications. These condensers consist of a cylindrical shell with a bundle of tubes running horizontally through it. These tubes are typically made of materials that facilitate efficient heat exchange, such as stainless steel or copper.
PRODUCTS GALLERY


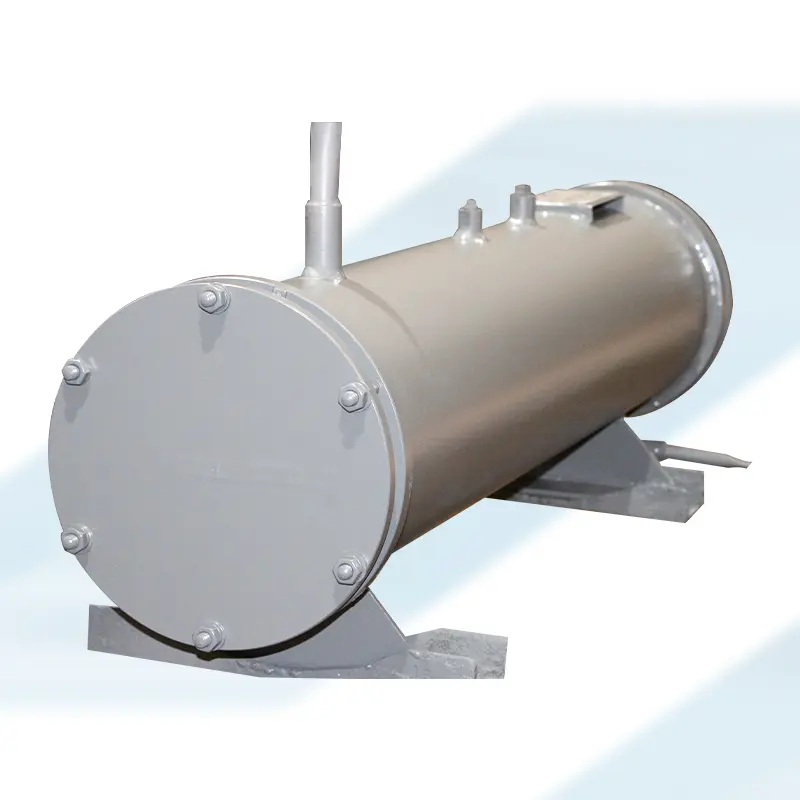
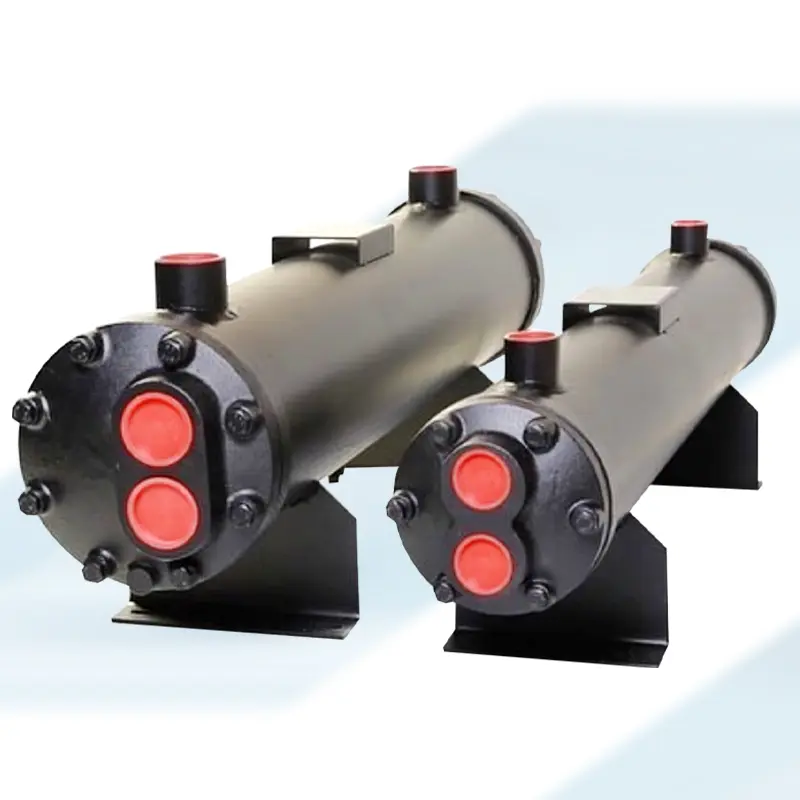
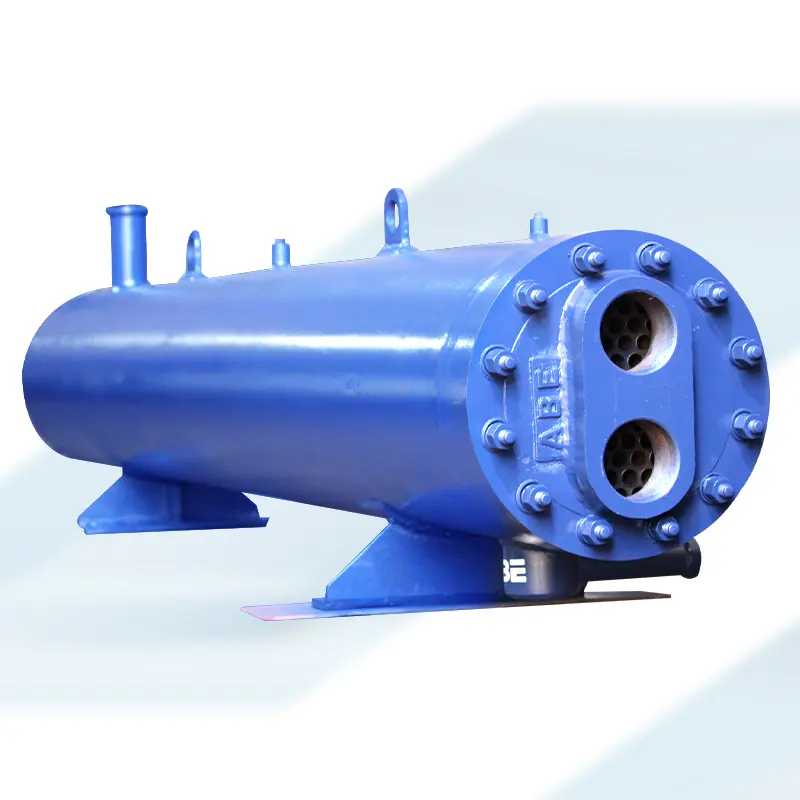
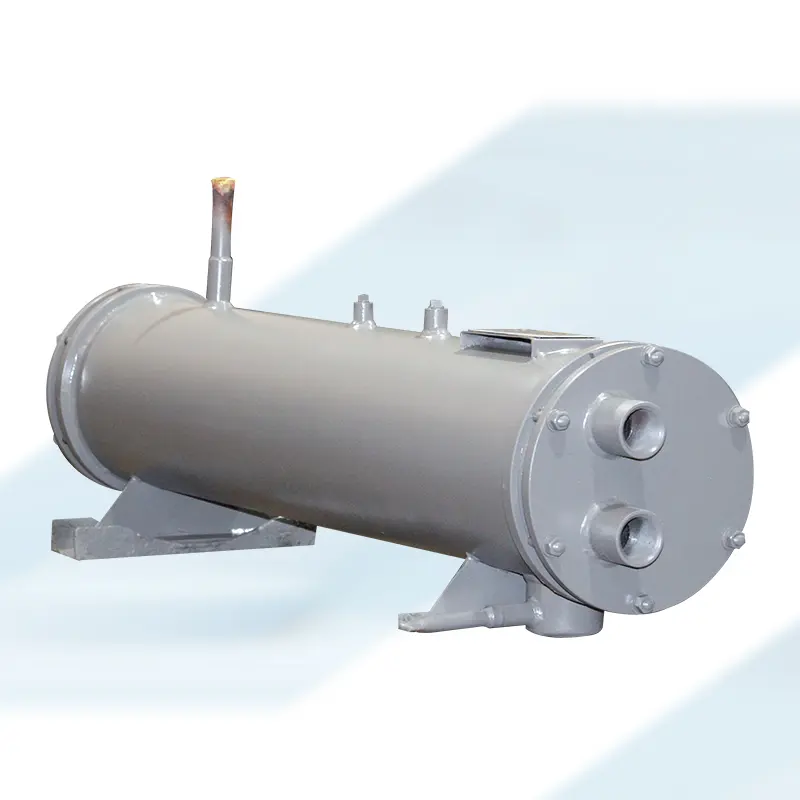
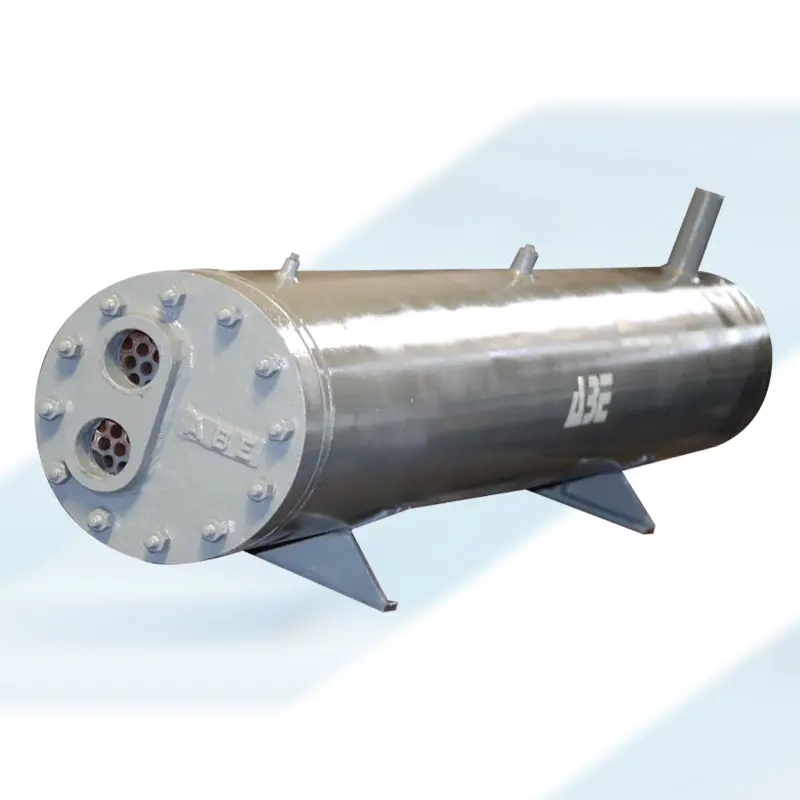
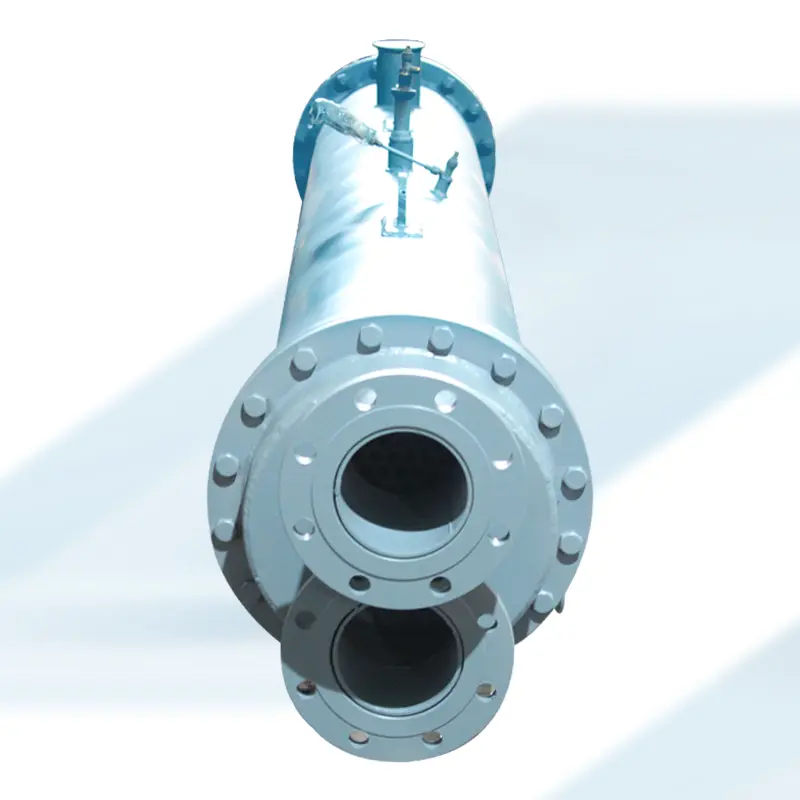
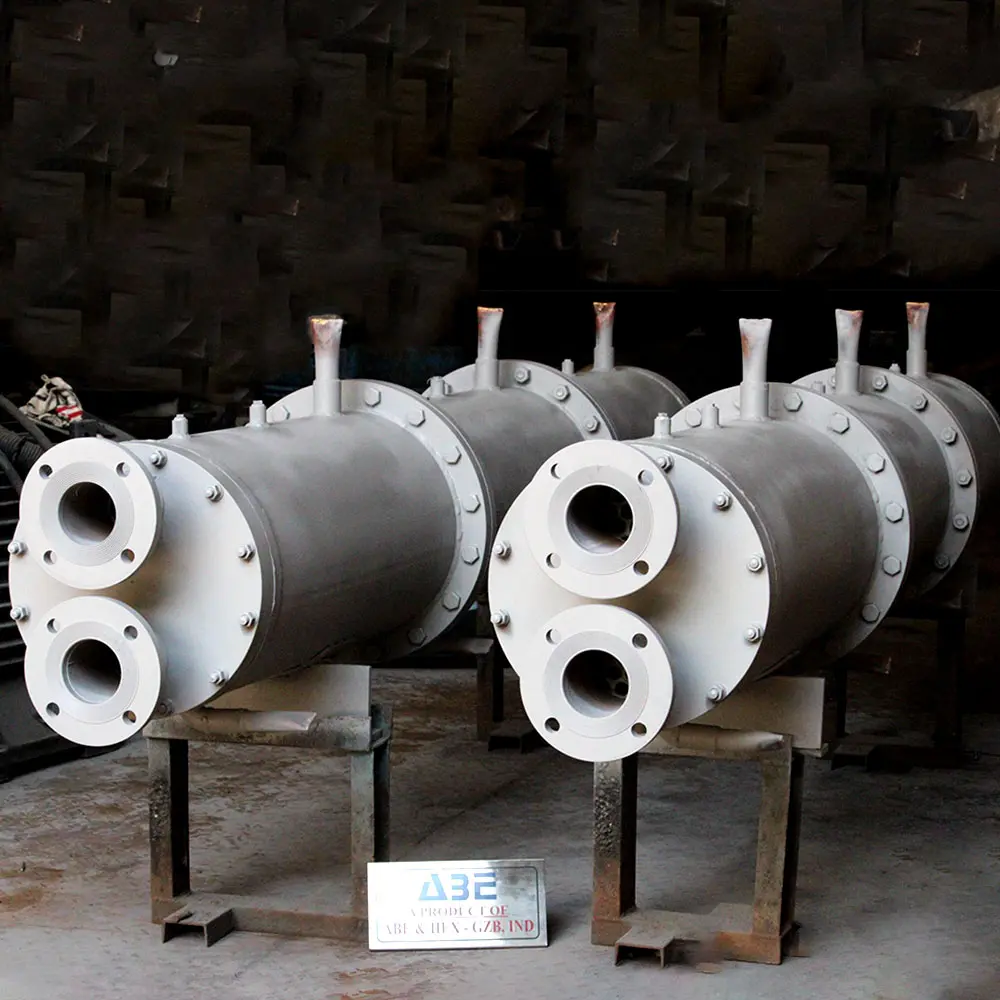
Efficient Cooling with Horizontal Shell and Tube Condensers
With a heritage rooted in excellence, we’ve honed our expertise over several years to become one of the top Horizontal Shell and Tube Condenser Suppliers in India. Our products are highly regarded in the market due to their extended lifespan, and minimal maintenance requirements. To uphold the quality of our products, our team of professionals adheres to quality assurance practices and employs cutting-edge testing methodologies.
Investing in a high-quality Copper Shell And Tube Heat Exchanger is not just a choice for today, but a smart move for the future of your industrial operations. So contact Abe and Hex India Private Limited today and discuss your specific requirements about these condensers.
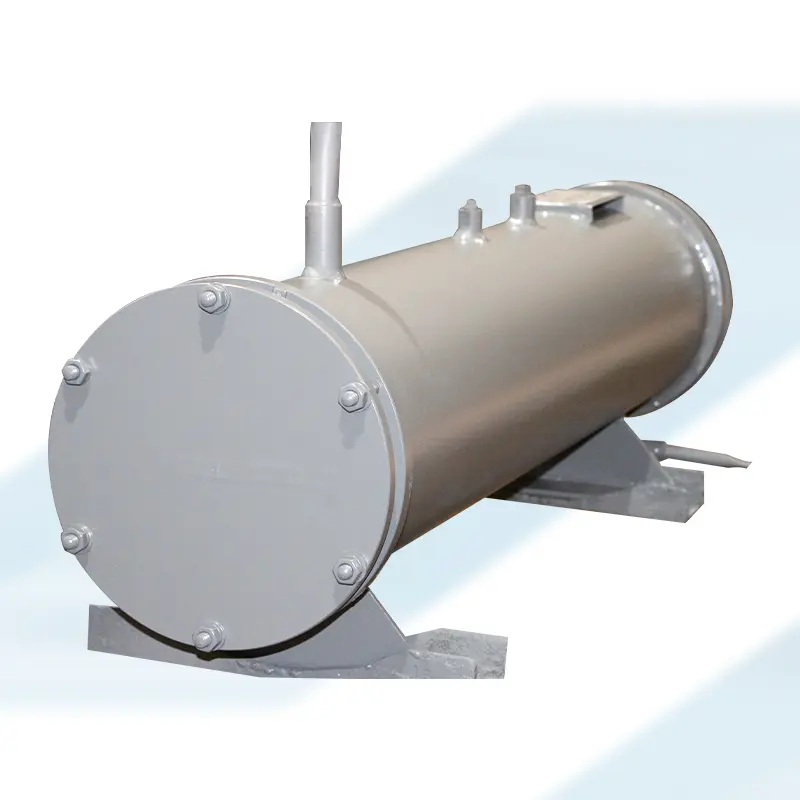
Key Features
- Incredibly versatile
- High thermal efficiency
- Easy maintenance and cleaning
- Large surface area for heat transfer
- Constructed from high-quality materials
- Withstand harsh industrial environments
- Resistance to high pressure and temperature
Applications
- Refrigeration
- Hydraulic systems
- Petrochemical industry
- Chemical processing systems
- Condensing steam in power plants
- Cooling of compressor and engines
SPECIFICATIONS
The condenser capacity should match the chiller system’s cooling requirements.
The tube design for shell and tube condensers can vary, including finned tubes or smooth tubes, depending on efficiency and heat transmission needs.
Water-cooled condensers are sensitive to the quality of the water. To avoid scaling or corrosion, it is critical to monitor and maintain the quality of the cooling water.
- Shell and Tube Condenser: This condenser has tubes through which the refrigerant flows and a shell for water to flow over.
- Plate Heat Exchanger: A plate heat exchanger is used in some chiller systems as a condenser, which is both small and effective.
The water-cooled condenser should be constructed to support a specified cooling water flow rate, which is determined by the capacity of the chiller and the required temperature differential.
To lower running expenses, look for energy-efficient designs and features.
The condenser’s size and physical footprint should fit within the available space in the chiller plant.
Easy access to the condenser for maintenance and cleaning is critical to ensuring its long-term functioning.
Determine whether the condenser has integrated controls and monitoring systems for efficient operation and problem detection.
To aid heat exchange or maintain adequate water flow, some condenser designs may require fans or pumps.
Materials used to build this type of condenser are resistant to corrosion and withstand environmental conditions.
Make sure that the condenser is compatible with the refrigerant type used in the chiller system.
Always follow the manufacturer’s installation, operating, and maintenance instructions.
The heat transfer surface area of the condenser is intended to efficiently transfer heat from the refrigerant to the cooling water.
Ensure that the condenser conforms with all applicable environmental rules and safety requirements.
The condenser should have inlet and outlet connections for the flow of refrigerant within and out of it.
The condenser will be designed with Inlet and outlet connections for the supply and return of cooling water.
QUALITY OF WATER COOLED CONDENSER
Exceptional condenser units sometimes feature integrated sensors and controls, enabling constant real-time monitoring and precise adjustment of operating parameters.