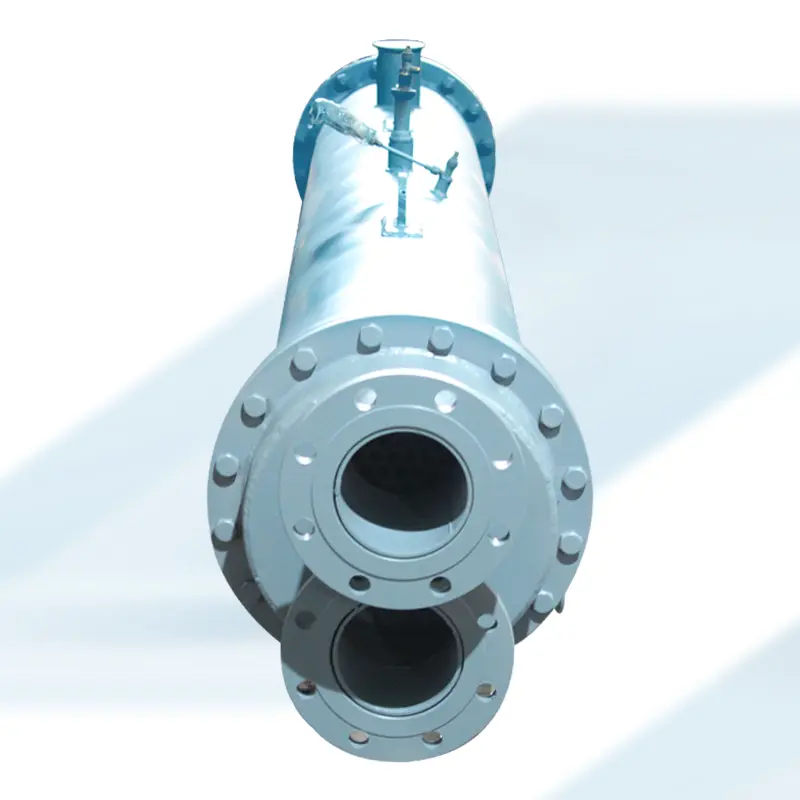
Shell and Tube Condenser: Precision Engineering for Superior Performance
Efficiency and reliability are paramount when it comes to condenser systems, and our Shell and Tube Condenser stands as an example of both. These condensers are designed to excel in heat exchange applications and meet the most demanding industry requirements.
Abe & Hex India Private Limited is a leading manufacturer and supplier of top-tier shell tube condensers in India. Our commitment to quality has earned us the trust and appreciation of countless customers, solidifying our position as one of the trusted Shell and Tube Condenser Manufacturers in India.
Our tube in tube water cooled condensers are built using premium-grade raw materials in our sophisticated manufacturing facility. We exclusively source the raw materials from trusted vendors to ensure durability and guarantee optimal performance of our products under the most challenging operating conditions.
PRODUCTS GALLERY

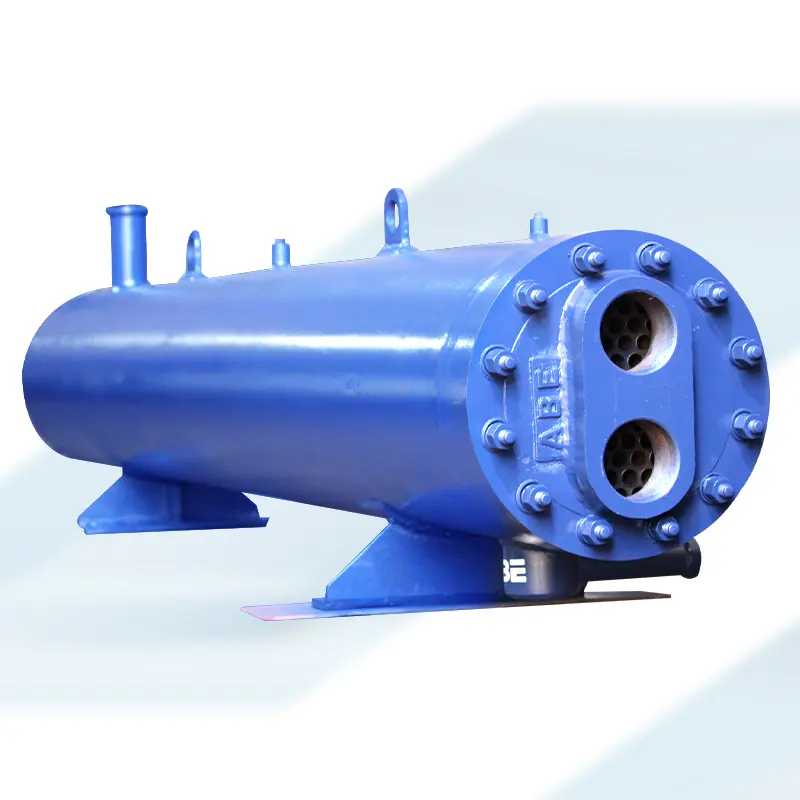
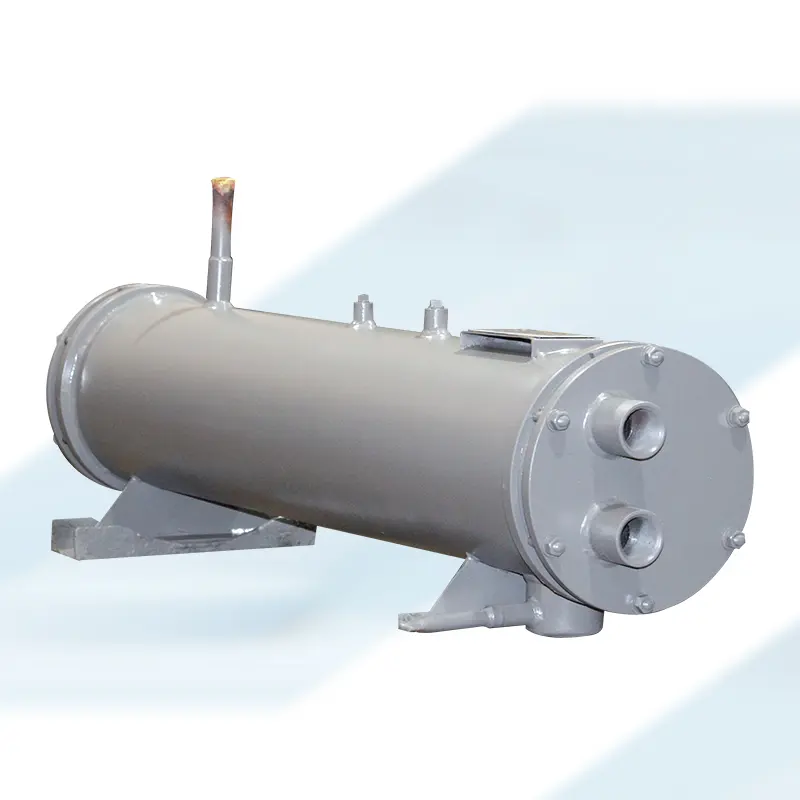
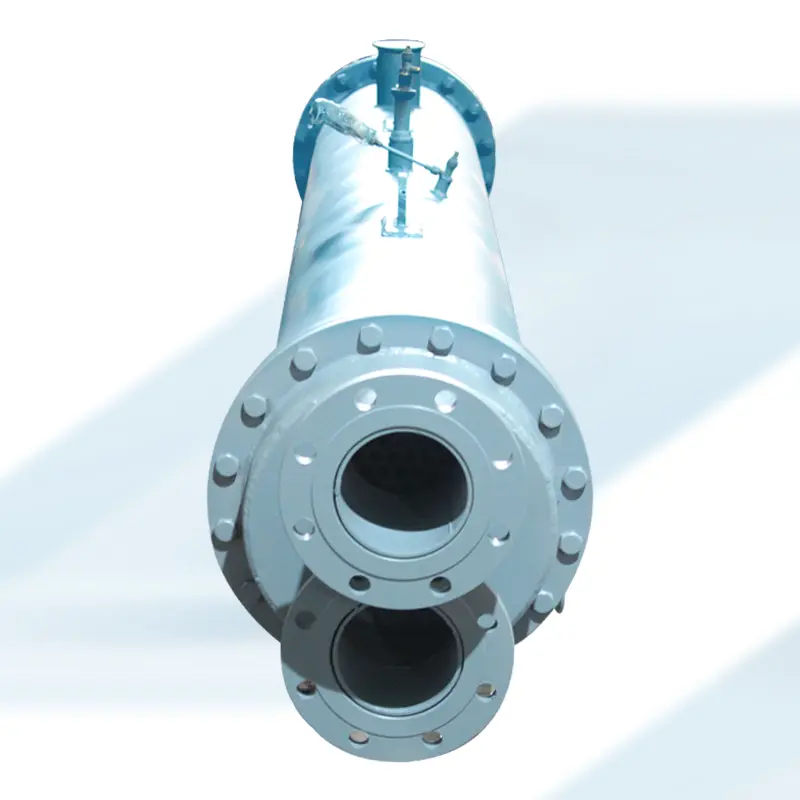
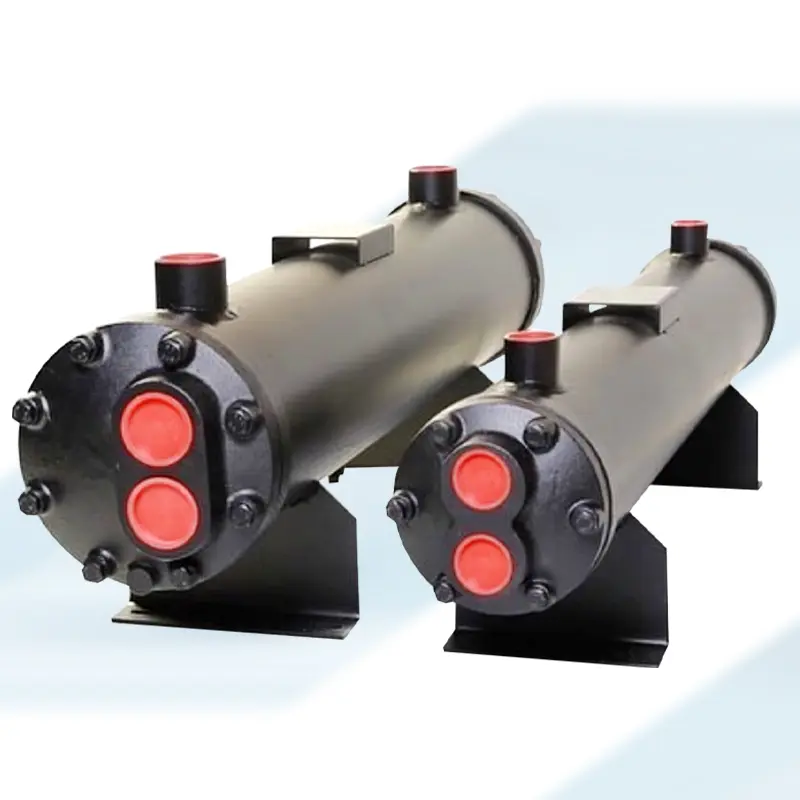
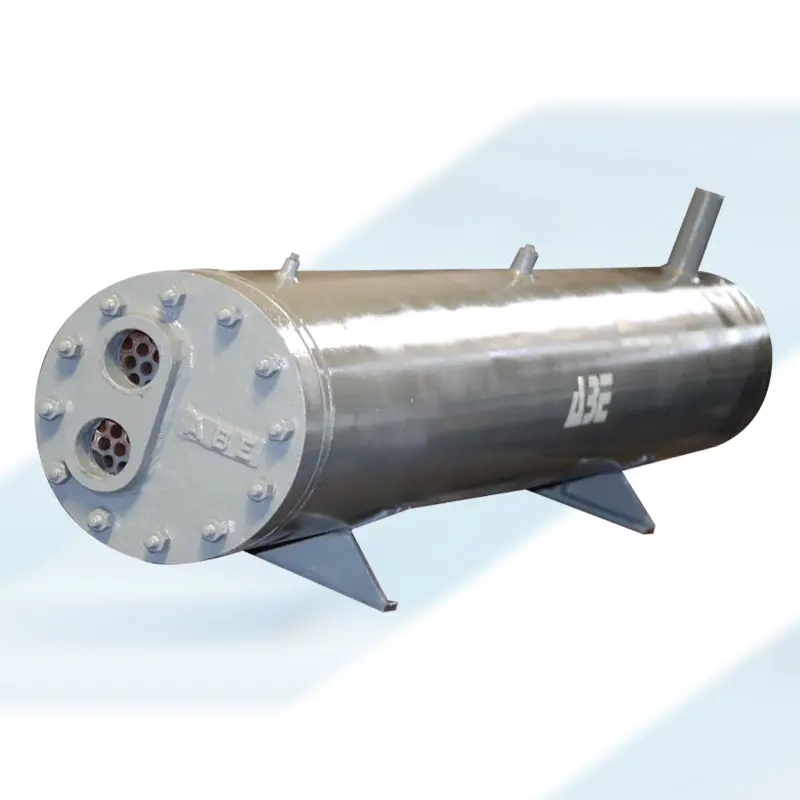

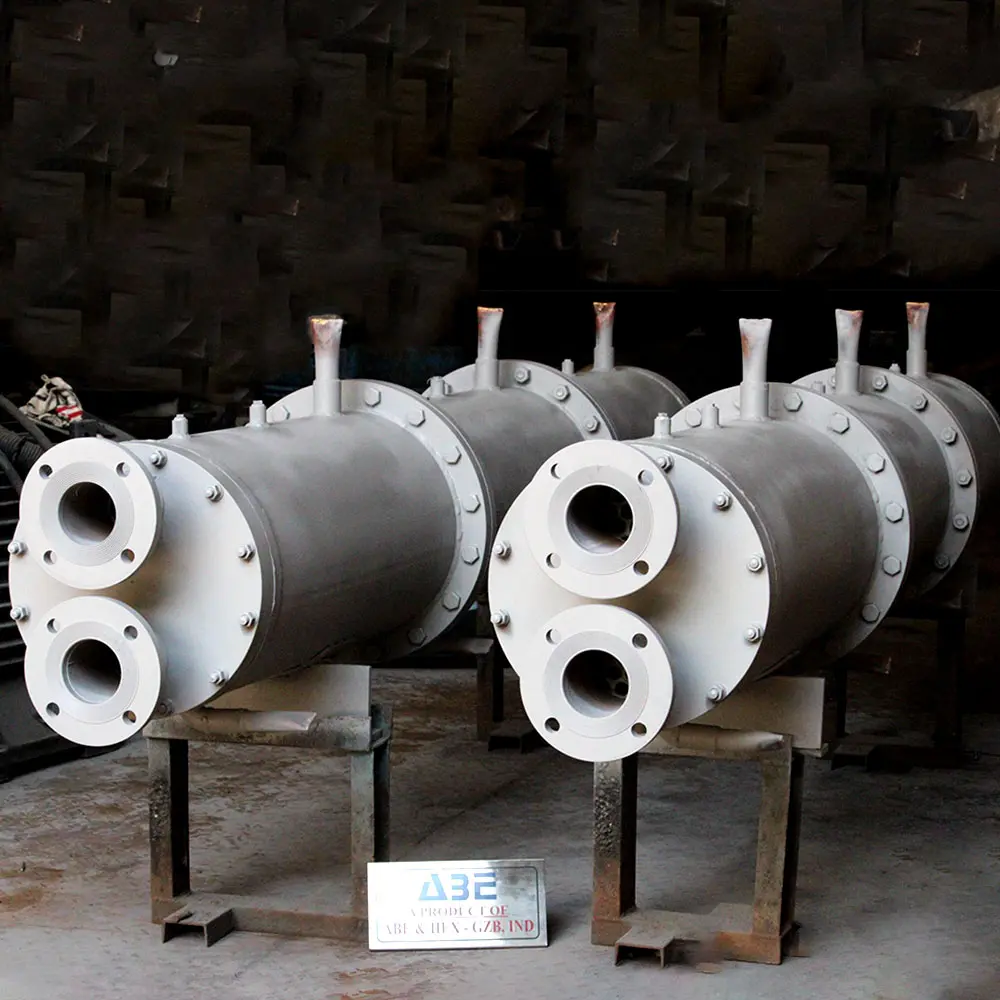
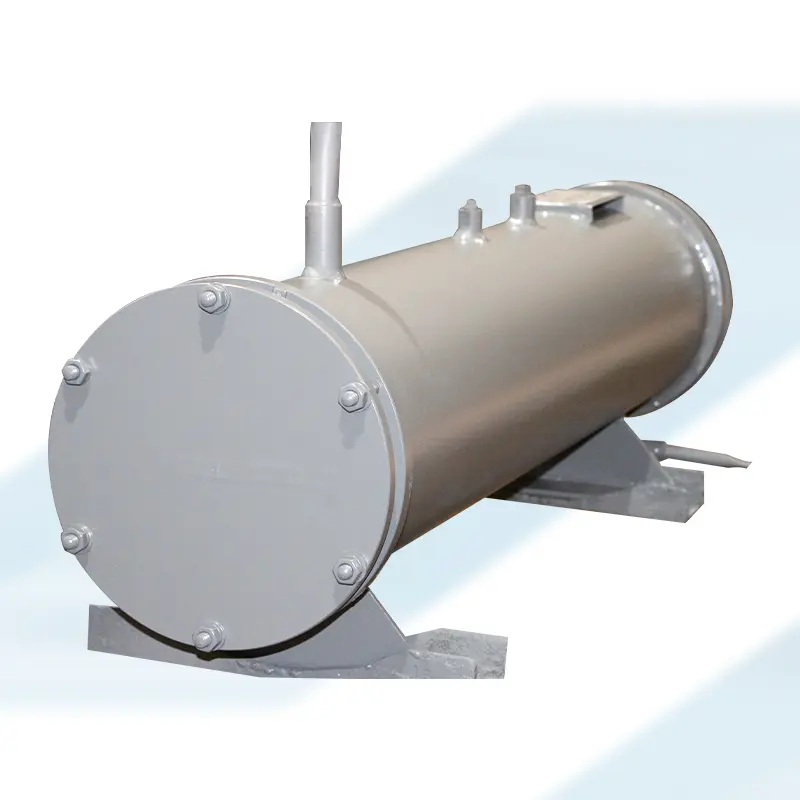
Explore Our Expertly Crafted Shell and Tube Condenser
As leading Sheel and Tube Condenser Suppliers in India, we adhere rigorously to stringent industrial standards, ensuring that each product leaving our facility is of the highest quality. Your satisfaction is our priority, and we take pride in delivering bespoke solutions according to the exact specifications given by you.
With years of expertise in condenser design and manufacturing, we take pride in being industry leaders. Our commitment to excellence, coupled with a relentless pursuit of innovation, sets us apart. When you choose our Shell and Tube Condenser, you’re investing in a product that exemplifies quality and performance.

Key Features
- Customization options
- Hassle-free maintenance
- Innovative and robust design
- Optimal heat transfer efficiency
- Minimized energy consumption
- Made from high-grade materials
- Versatile solutions for cooling needs
- Built with precision and tested rigorously
- Guarantees longevity and resilience in industrial environments
Applications
- Hospitals
- Data centers
- Laboratories
- Manufacturing sector
- Food processing sector
- Power generation plants
- Pharmaceutical production
- Plastic and chemical processing sector
SPECIFICATIONS
The condenser’s capacity must align with the chiller system’s cooling load, usually quantified in tons or kilowatts.
The tube arrangement in shell and tube condensers can take various forms, whether finned or smooth tubes, and this selection hinges on the efficiency and heat transfer prerequisites.
The effectiveness of water-cooled condensers is linked to water quality. It’s of utmost importance to systematically monitor and preserve the standard of the cooling water to thwart issues like scaling or corrosion.
- Shell and Tube Condenser: This is a common type. It has tubes through which refrigerant flows while water flows over these tubes.
- Plate Heat Exchanger: Some chillers use these exchangers as condensers as they’re small and work well.
Consider energy-efficient designs and attributes as a means to decrease operating expenses.
It is imperative that the condenser’s size and physical dimensions align with the designated space in the chiller plant.
The water-cooled condenser should be fashioned to accommodate a specific flow rate of cooling water, a value hinging on the chiller’s capacity and the desired temperature differential.
Evaluate if the condenser is equipped with integrated controls and monitoring systems to ensure smooth operation and prompt fault detection.
Depending on the condenser design, fans or pumps might be necessary to facilitate heat exchange or sustain appropriate water flow.
The condenser is usually constructed from corrosion-resistant materials like copper, aluminum, or stainless steel.
It is crucial to consistently comply with the manufacturer’s guidelines for installation, operation, and care.
The surface area for heat transfer in the condenser is engineered to effectively move heat from the refrigerant to the cooling water.
Ensuring convenient access to the condenser for regular maintenance and cleaning is crucial for optimizing its longevity and performance.
Ensure that the condenser is designed to work seamlessly with the type of refrigerant employed in the chiller system.
Guarantee the condenser conforms to environmental regulations and meets safety standards.
This condenser is equipped with dedicated ports for the ingress and egress of refrigerant, ensuring efficient flow within the system.
This condenser boasts provisions for both the intake and discharge of cooling water.