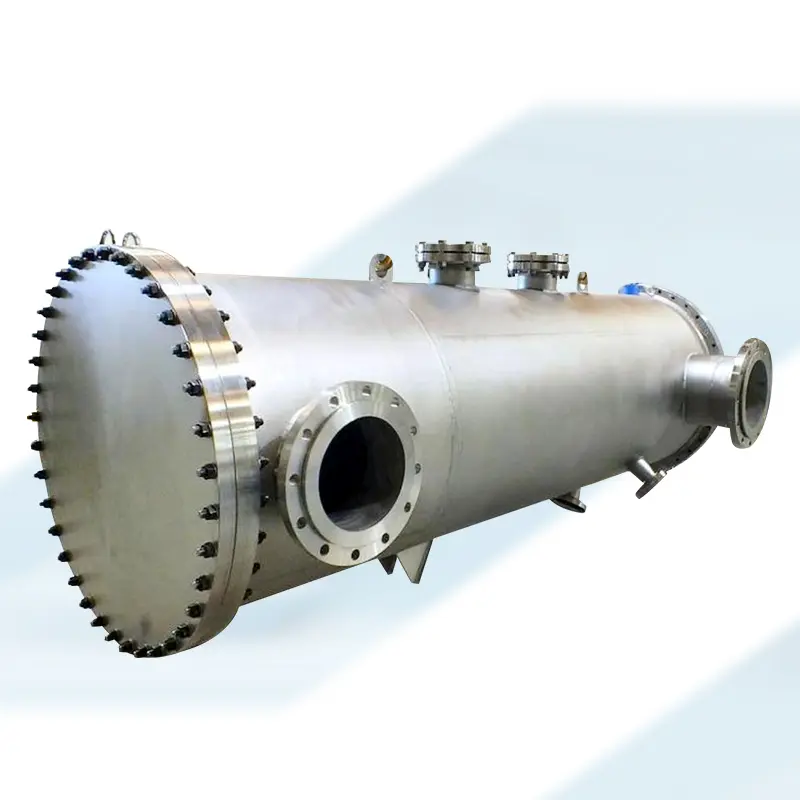
Providing Premium Stainless Steel Shell And Tube Condenser
Abe and Hex India Private Limited takes pride in being a leading manufacturer and supplier of top-tier condensers & heat exchangers. One of the well-known products that we offer is the Stainless Steel Shell and Tube Condenser.
The outer shell of this condenser is made from high-quality stainless steel, providing excellent corrosion resistance and ensuring a long lifespan. Inside, a series of tubes facilitate the exchange of heat between different fluids, allowing for efficient cooling or heating processes. Thanks to its robust construction, the SS Shell And Tube Condenser has become a staple in several industries.
Our commitment to precision engineering and quality helps us become one of the trusted Stainless Steel Shell and Tube Condenser Manufacturers in India. With our state-of-the-art manufacturing unit, we bring you a product that stands out for its quality and reliability.
PRODUCTS GALLERY
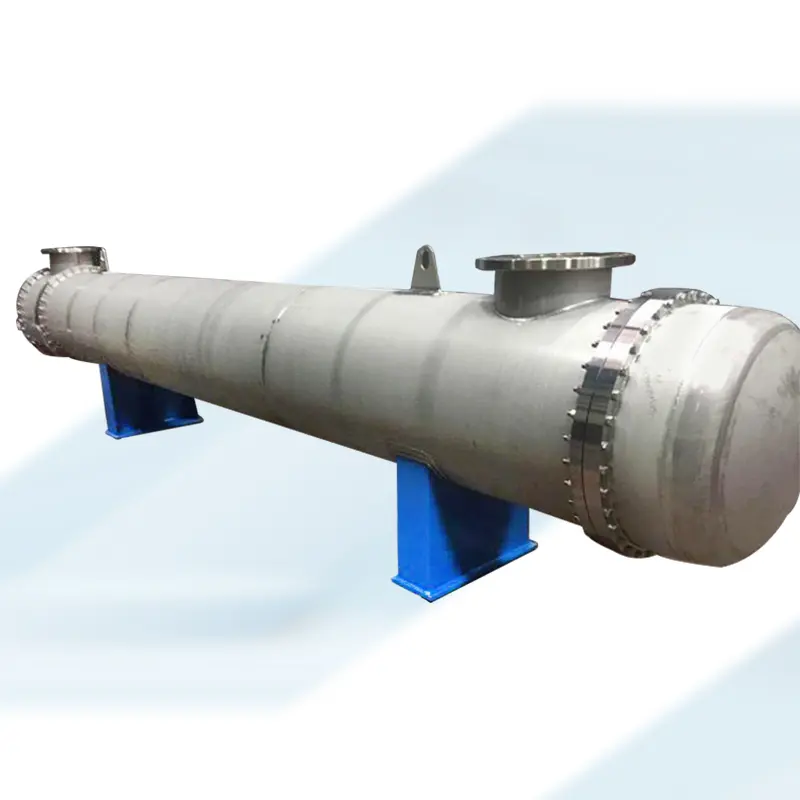
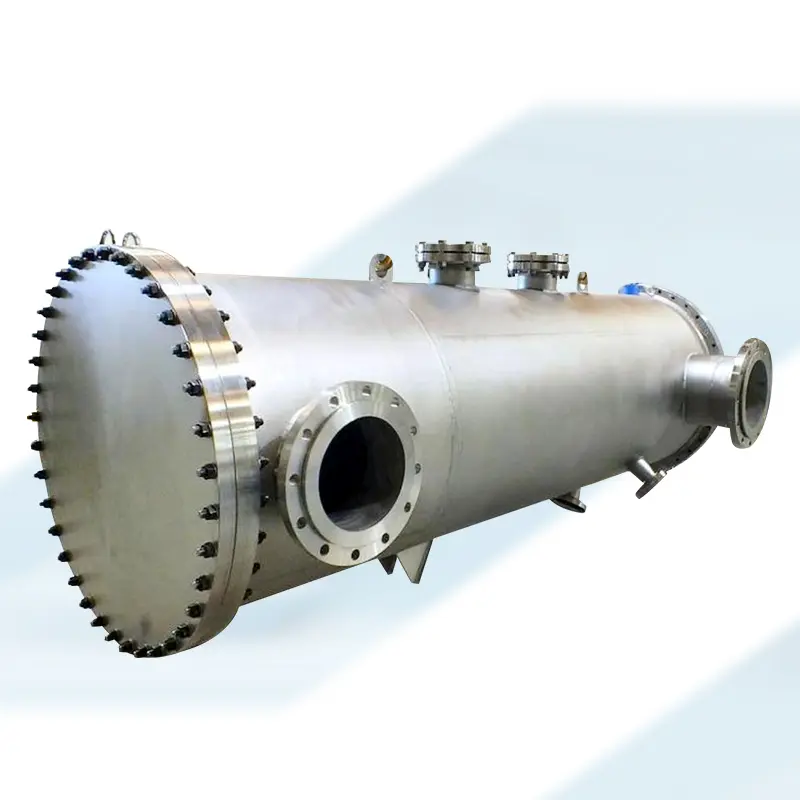
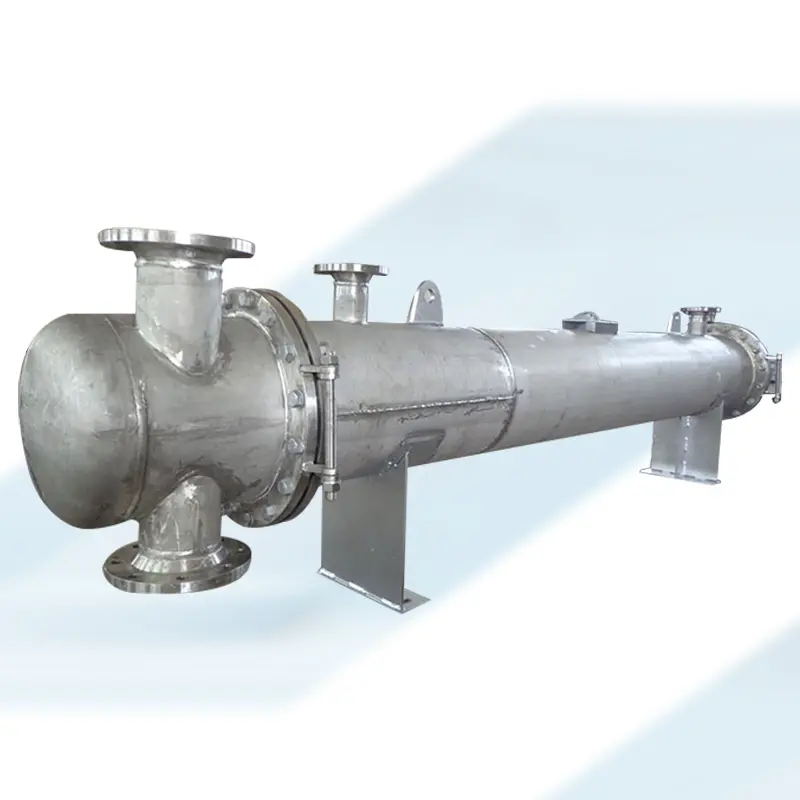
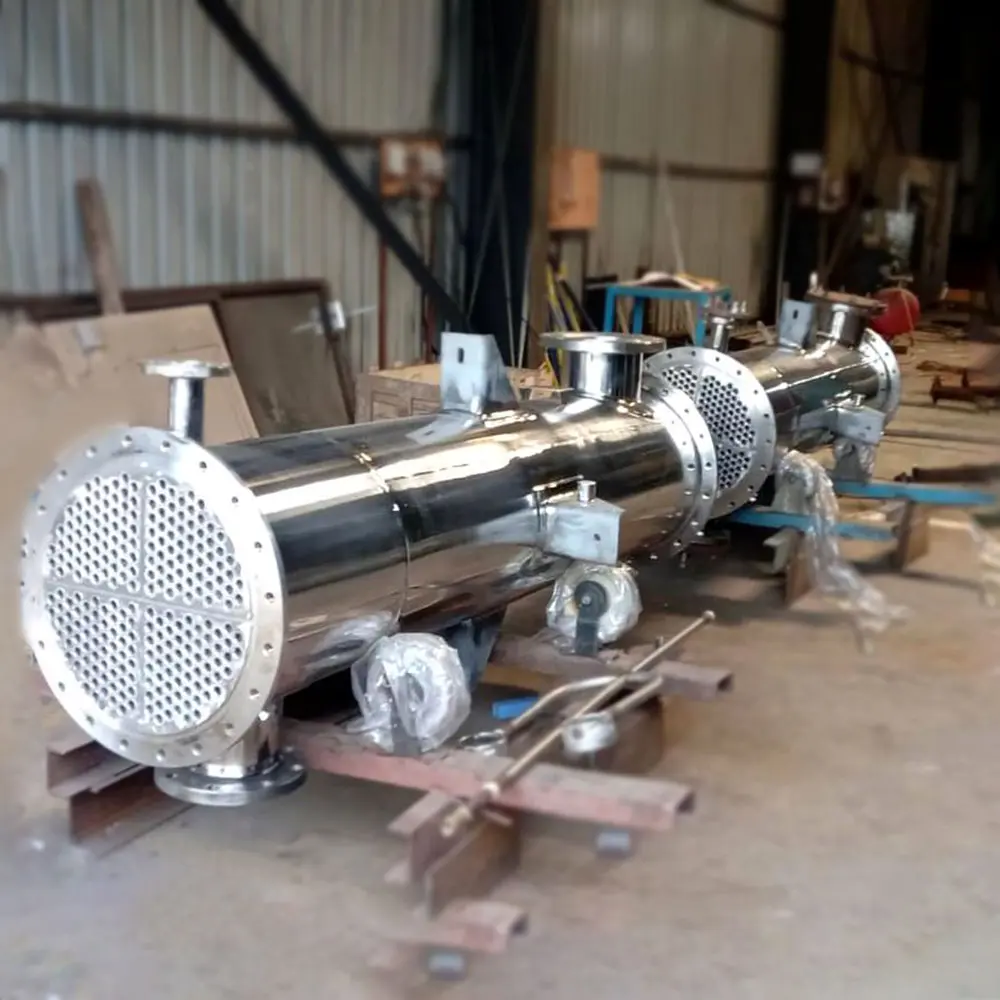
Choose From the Top Stainless Steel Shell And Tube Condenser Brands
Leveraging our cutting-edge facility, we craft these shell and tube heat condensers from top-tier raw materials sourced from reliable market vendors. Our team of quality assessors rigorously scrutinizes every stage of production utilizing state-of-the-art testing equipment. Furthermore, we offer customization in both design and packaging services.
Choose reputed Stainless Steel Shell and Tube Condenser Suppliers in India for a reliable, efficient, and durable solution to your heat exchange needs. Contact us today to learn more about how we can tailor a shell and tube surface condenser to meet your unique needs. You can also explore our other products such as shell and coil condensers on our website.
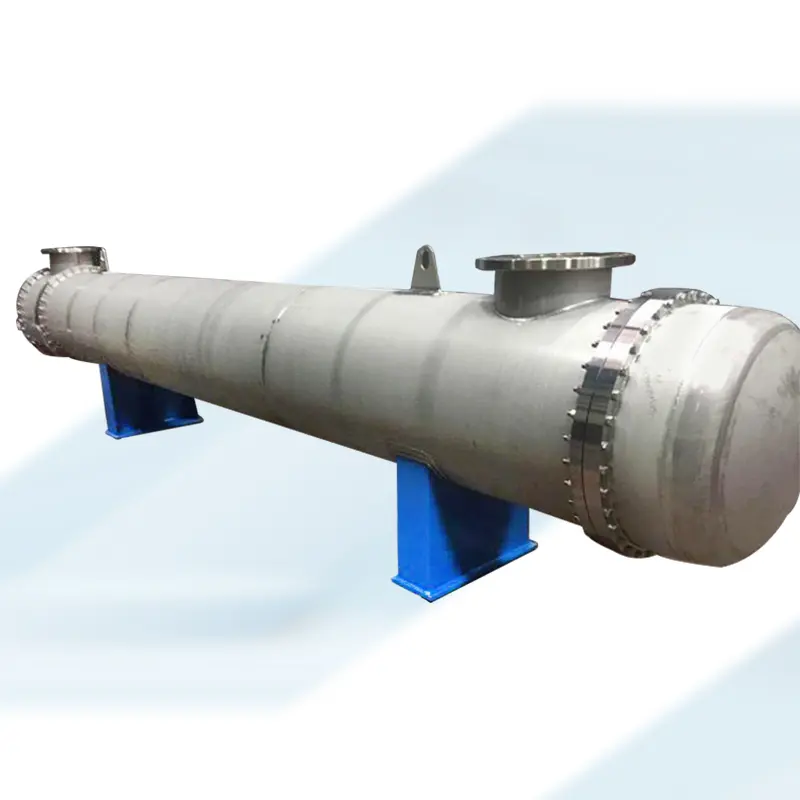
Key Features
- Easy Maintenance
- Trust in Excellence
- Customization Options
- Robust Shell and Tube Design
- High Heat Transfer Efficiency
Applications
- Thermal plants
- Exhaust systems
- Waste heat recovery
- Heat and power plants
- Foundries and steel processing
SPECIFICATIONS
The condenser capacity should be sufficient to handle the chiller system’s cooling loads.
Depending on efficiency and heat transfer requirements, the tube design for shell and tube condensers can vary, including finned tubes or smooth tubes.
Water-cooled condensers are sensitive to water quality. It is vital to check and maintain the cooling quality to avoid scaling or corrosion.
- Shell and Tube Condenser: In this type, the refrigerant moves through the tubes while water flows around them in a shell.
- Plate Heat Exchanger: Some chiller systems feature plate heat exchangers as condensers. These are small and work well.
The water-cooled condenser should be built to handle a certain cooling water flow rate defined by the chiller’s capacity and the needed temperature difference.
Look for energy-efficient designs and features to save operating costs.
The size and physical footprint of the condenser should be compatible with the available space in the chiller plant.
The ability to easily access the condenser for maintenance and cleaning is vital to guaranteeing its long-term operation.
Check to see if the condenser has integrated controls and monitoring systems to ensure efficient operation and problem identification.
Some condenser designs may require fans or pumps to promote heat exchange or maintain enough water flow.
This type of condenser is built of durable and corrosion-resistant materials, such as copper, aluminum, and stainless steel.
Check that the condenser is compatible with the kind of refrigerant used in the chiller system.
Always follow the installation, operating, and maintenance instructions provided by the manufacturer.
The condenser’s heat transfer surface area is designed to efficiently transfer heat from the refrigerant to the cooling water.
Check that the condenser complies with all applicable environmental and safety regulations.
For the flow of refrigerant within the condenser, it should have inlet and outlet connections.
For the supply and return of cooling water, the condenser will have inlet and outlet connectors.
QUALITY OF WATER COOLED CONDENSER
Fabricated with top-tier materials and meticulous attention to detail, a water-cooled condenser is tailored for enduring performance, thereby reducing the demand for frequent replacements.
The condenser’s design and construction should guarantee a high level of dependability, effectively mitigating any potential for breakdowns or failures that could disrupt the cooling process.
When creating the condenser, opt for materials of superior quality like stainless steel, copper, or aluminum to guarantee its prolonged performance and resistance to corrosion.
A proficiently designed condenser is integral to achieving optimal system energy efficiency. Utilizing top-tier materials and design can lead to a significant reduction in energy consumption.
Condensers of superior grade are fashioned for simplicity in maintenance. They provide accessible points for cleaning and inspection, ensuring that upkeep is uncomplicated.
The effectiveness of a high-grade condenser lies in its ability to swiftly convey heat from the refrigerant to the cooling water, wherein the design and surface area of the condenser tubes or plates hold paramount importance.
A manufacturer or supplier’s preparedness to offer warranty and support is a strong indicator of the condenser’s quality.
Excellent water-cooled condensers require thorough water quality regulation. This involves procedures to hinder corrosion, manage algae and biofilm growth, and supervise water chemistry to avert scaling.
The condenser is expected to satisfy industry-specific requirements for safety, environmental impact, and operational efficacy, as dictated by relevant regulations.
Exceptional capacitors may possess noise and vibration management capabilities, ensuring trouble-free performance.
Ensuring compatibility between the condenser and the refrigerant utilized in the chiller system is vital for achieving optimal performance and preventing issues like refrigerant leakage.
The condenser should be carefully built and expertly assembled to reduce the likelihood of leaks, ensure an effective seal, and uphold structural integrity.
A high-grade condenser blueprint encompasses features to counter fouling and scaling. Fouling can hinder heat transfer efficiency and raise maintenance demands.
Select advanced condenser units may include built-in sensors and controls, allowing for continuous real-time monitoring and precise adjustment of operational settings.