
Stainless Steel Tube Condenser: Your Reliable Heat Exchange Solution!
Upgrade your industrial processes with our advanced Tube Condenser, designed to meet your exacting requirements. Our stainless steel tube condensers are engineered with precision, setting new standards in condenser technology.
At Abe & Hex India Private Limited, we leverage our state-of-the-art manufacturing facility and cutting-edge technology to produce top-tier tube condensers. As one of the leading Tube Condenser Manufacturers in India, we have garnered a reputation for excellence.
This condenser features a tube-in-tube design for optimal heat exchange between fluids. Our tube in tube condenser is crafted with premium quality raw materials such as stainless steel. The raw material is sourced from trusted vendors available in the market to meet industrial standards and offers unmatched durability.
PRODUCTS GALLERY


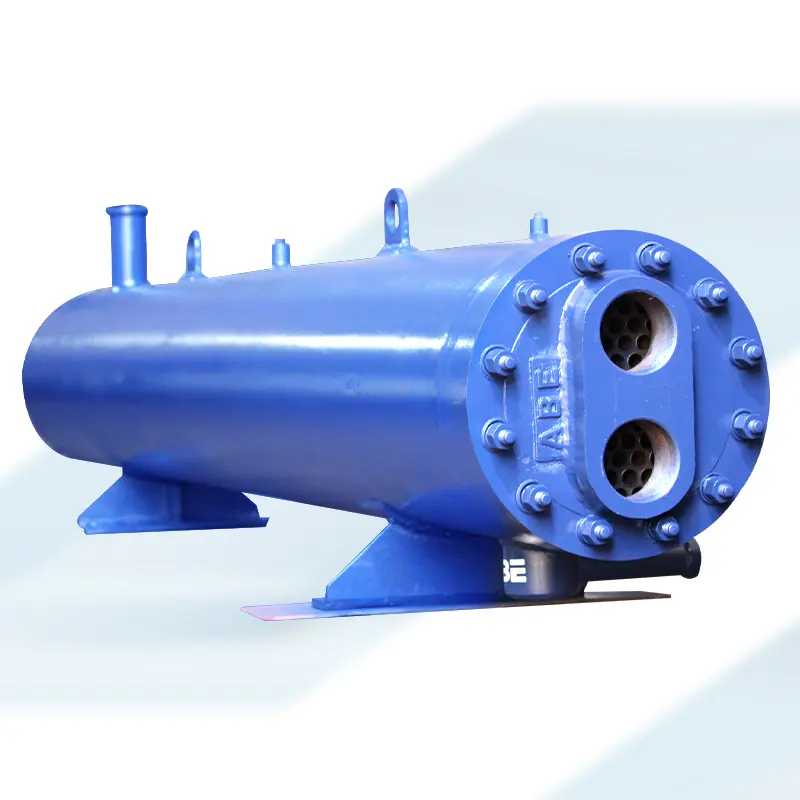
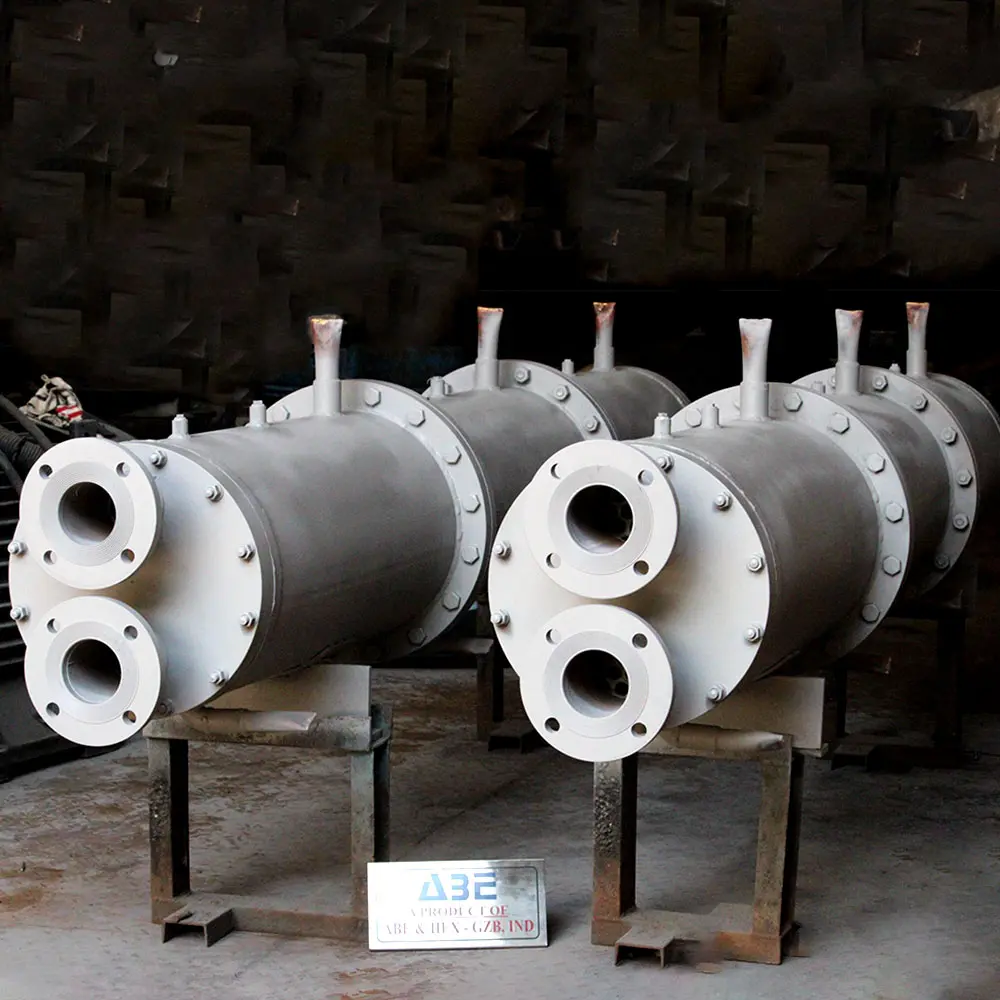
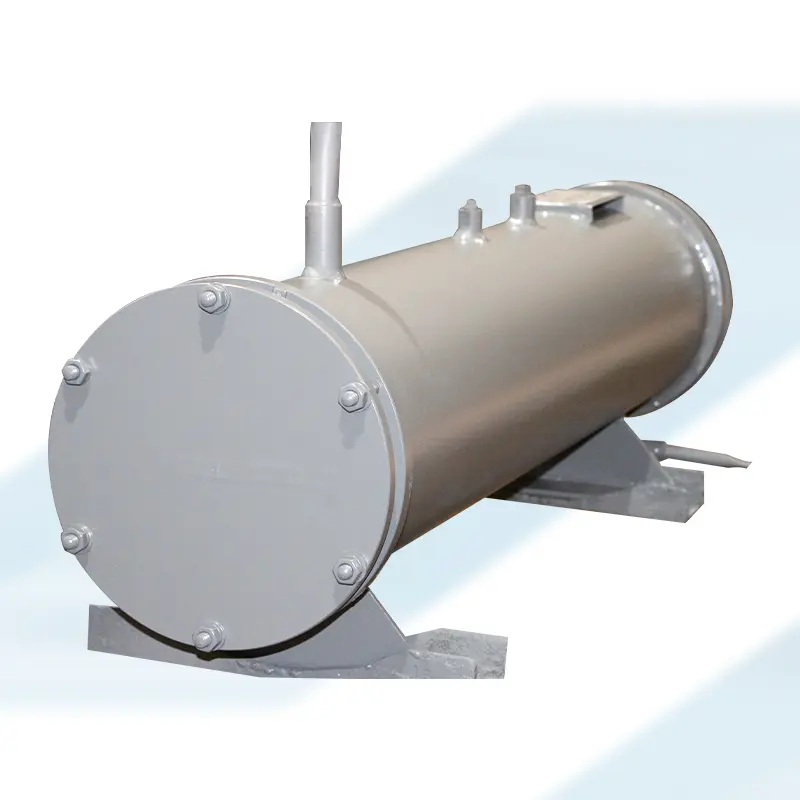
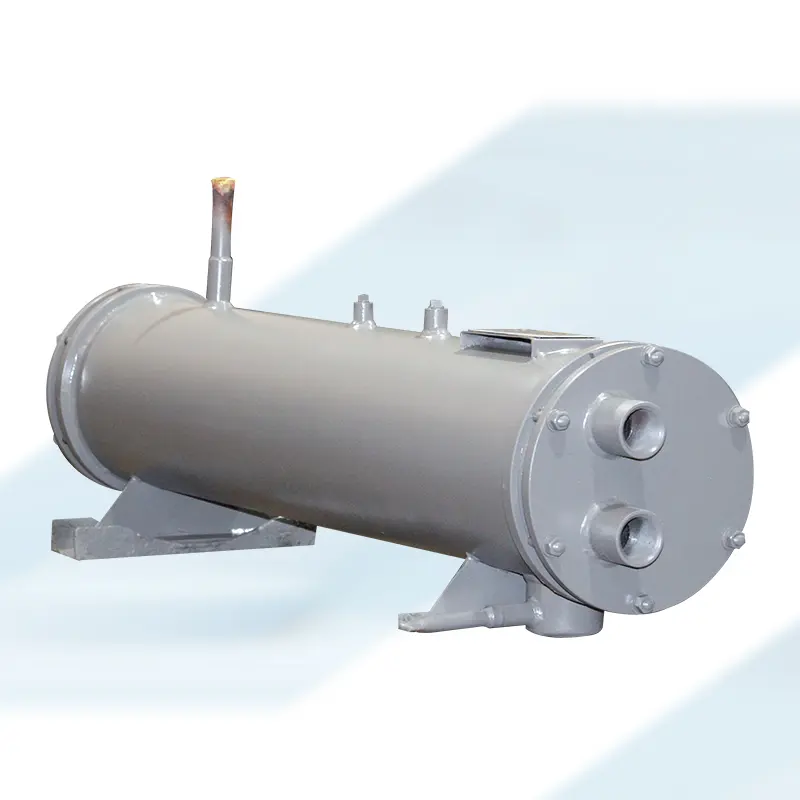
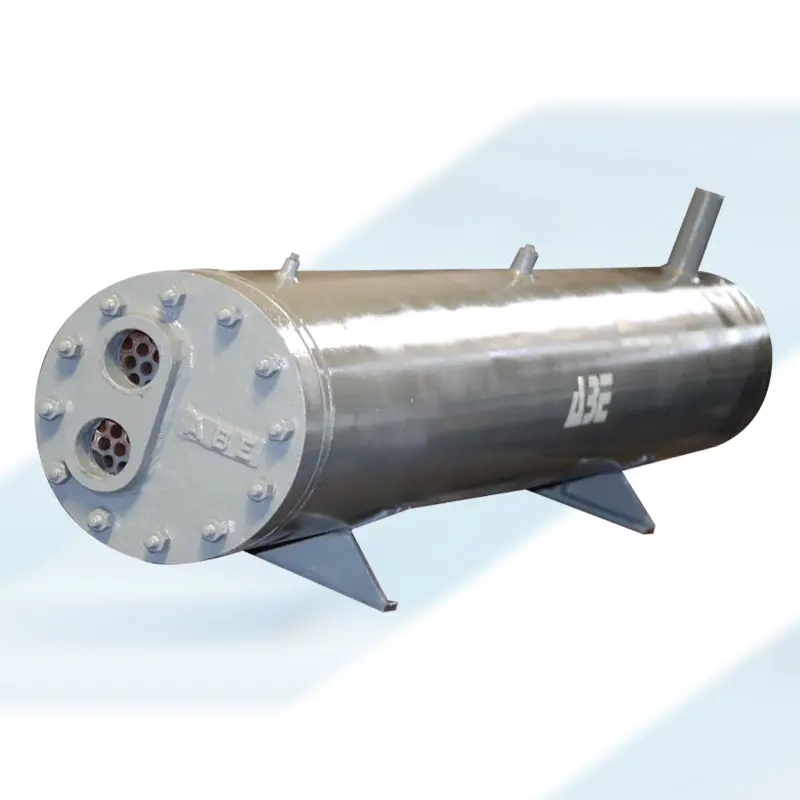
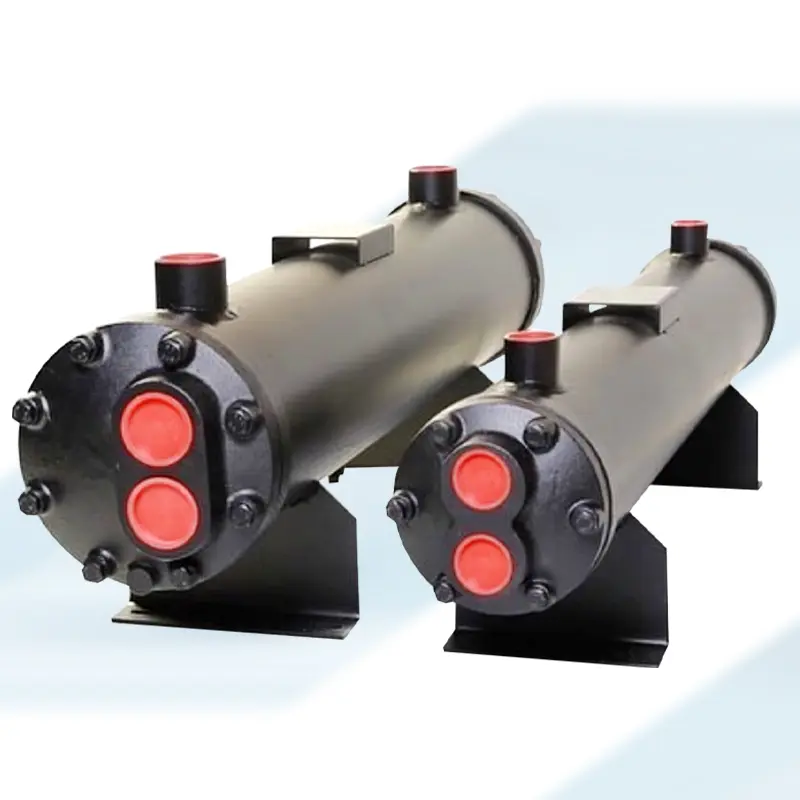
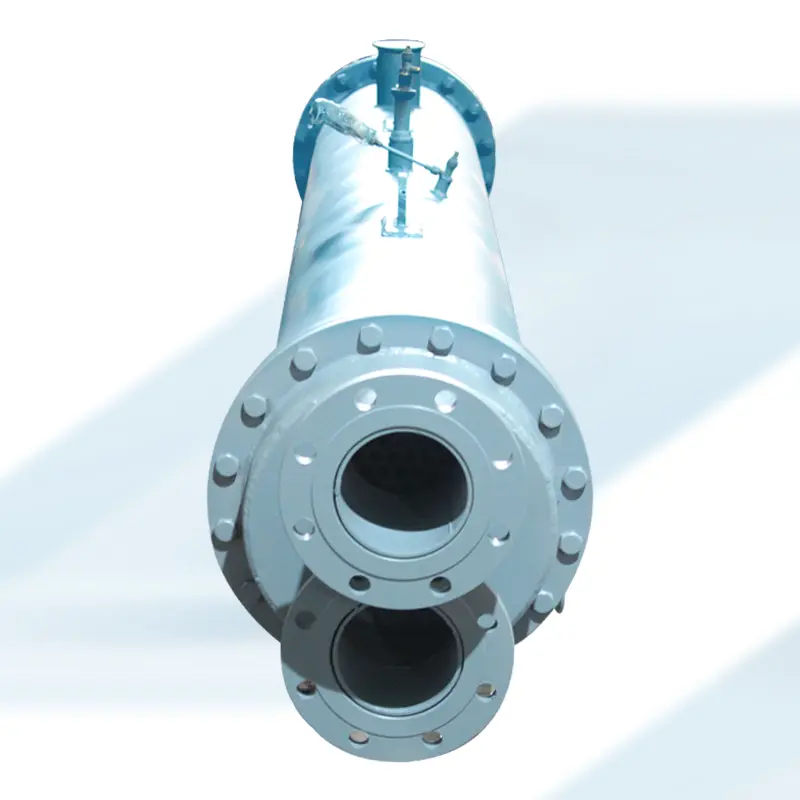
Invest in the High-Quality Tube Condenser: Made With Durable Materials!
Our SS Tube Condensers are trusted and appreciated by customers across various industries. This acclaim has propelled us to the forefront of the market and helped us become one of the top Tube Condenser Suppliers in India.
We work closely with our clients to provide customized stainless steel condenser tubes that align with their specific requirements. Whether it’s the innovative tube-in-tube design or the double tube condenser configuration, our range of products ensures optimal performance in diverse applications. Order your stainless steel tube condenser from Abe & Hex India today and elevate your operations to new heights of efficiency and reliability.
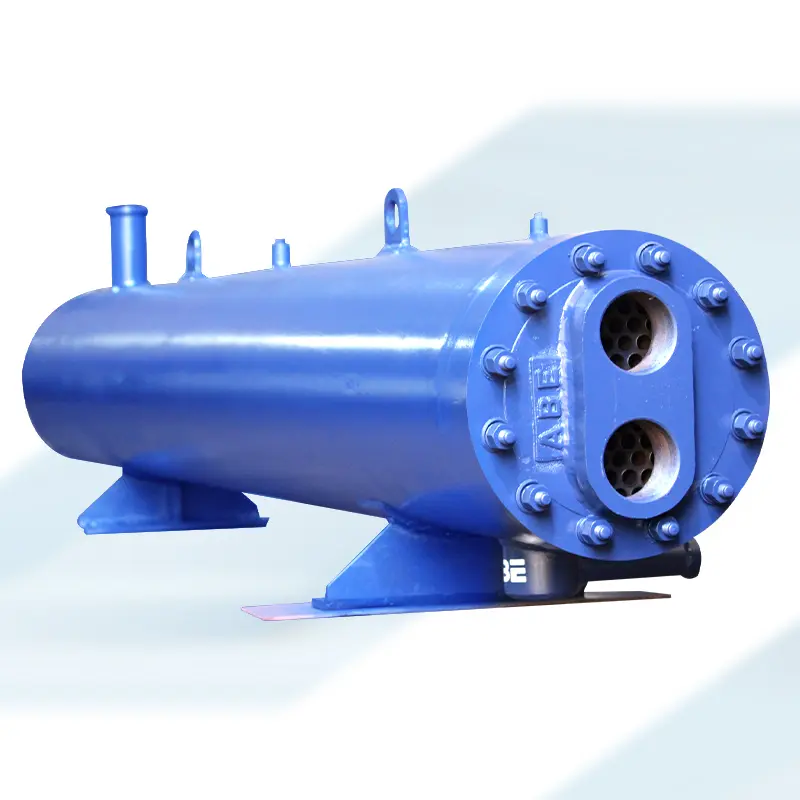
Key Features
- Unmatched durability
- Robust construction
- Double tube configuration
- Resistance against corrosion
- Maximized surface area contact
- Compact and low-maintenance
- Unparalleled heat transfer capabilities
- Crafted from premium-grade stainless steel
- Tube-in-tube design for optimized heat exchange
Applications
- Power Plants
- HVAC Systems
- Petrochemical Industry
- Food and Beverage Industry
- Chemical Processing Plants
- Food Processing and Preservation
- Brewing and Distilling Applications
- Pharmaceutical Manufacturing Sector
- Refrigeration and Air Conditioning Systems
SPECIFICATIONS
The condenser should be sized to match the cooling load of the chiller system, which is commonly measured in tons or kilowatts.
In the realm of shell and tube condensers, the tube configuration may differ, encompassing options like finned or smooth tubes, contingent upon the desired efficiency and heat transfer needs.
Water-cooled condensers can be affected by the quality of water they use. It’s crucial to consistently check and uphold the standard of the cooling water to avert issues like scaling or corrosion.
- Shell and Tube Condenser: This type of condenser is a typical design where the refrigerant moves through the tubes, and water moves over the tubes in a shell.
- Plate Heat Exchanger: Condensers in certain chiller systems are fulfilled by plate heat exchangers, prized for their efficiency and compact form.
Seek out designs and features that prioritize energy efficiency to minimize operational expenses.
Ensure that the condenser’s size and physical dimensions are a suitable match for the available space in the chiller plant.
The water-cooled condenser’s specifications must align with the designated flow rate of cooling water, contingent on both the chiller’s output and the preferred temperature variance.
Reflect on whether the condenser features integrated controls and monitoring systems to support effective operation and timely detection of faults.
Certain condenser configurations might necessitate the use of fans or pumps to enhance heat exchange or ensure optimal water circulation.
Copper, aluminum, or stainless steel, which have high resistance to corrosion, are the customary materials for crafting condensers.
It is imperative to adhere to the installation, operation, and maintenance instructions provided by the manufacturer at all times.
The condenser’s design ensures that its heat transfer surface area efficiently facilitates the movement of heat from the refrigerant to the cooling water.
Prioritizing convenient access to the condenser for maintenance and cleaning is essential for upholding its long-lasting performance.
Verify that the condenser is suitable for the refrigerant type employed in the chiller system.
Verify that the condenser adheres to both environmental protocols and safety criteria.
This condenser is outfitted with tailored ports to accommodate the entry and exit of refrigerant, ensuring an uninterrupted and efficient flow within the unit.
This condenser is characterized by its inlet and outlet connections, catering to both the supply and return of cooling water.